Industry Reports
Rotary kiln shell fabrication
Causes of cylinder deformation:
The rotary kiln shell is made of steel plates such as boilerplate and Q235C plate, requiring highly on dimensional accuracy and geometric tolerances.
1. If the output is too large, the wear of the kiln mouth cylinder material will increase, which will easily cause the overheating deformation of the cylinder body.
2. The heat flow is too large, the cooling zone is very short or even no, the working environment of the kiln mouth is bad, the temperature of the clinker out of the kiln is 1300-1400℃, and the secondary air temperature is 1000-2000℃
3. The temperature of the kiln body is too high, the thermal expansion is large, and the strength of the high-temperature resistant material is seriously attenuated
4. The loosening of the bolts of the kiln mouth guard plate causes the refractory material to fall off, thereby burning the cylinder.
5. Burning polluted soil, and improper treatment will cause serious corrosion to the cylinder, and in serious cases, the kiln will collapse.
6. The corrosion of the kiln shell by sulfur, phosphorus, and chlorine will not only reduce the strength of the kiln shell but also reduce the shaping of the steel and increase the brittleness of the steel, which may lead to the brittle failure of the kiln shell.
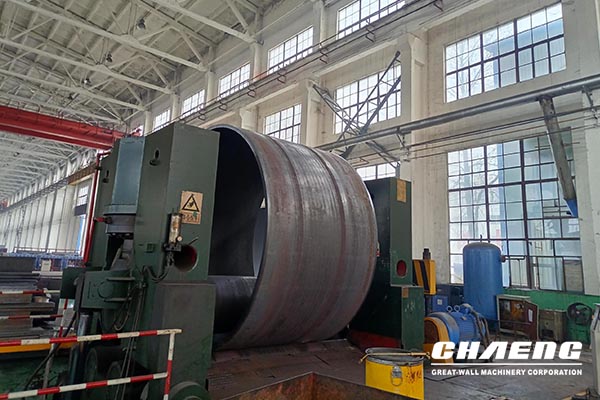
Due to transportation reasons, the rotary kiln is composed of shell segments. Because the outer circle of the kiln cylinder is not processed, the perpendicularity of the end face to the center of rotation cannot be directly measured. In the process design, the perpendicularity of the end face is converted into parallelism, and the coincidence of the axes at both ends according to the structure of the cylinder.
CHAENG adopts a local forming method to design specific manufacturing processes and welding methods of the single-segment cylinders according to the detailed requirements of the drawings. After the assembly and welding of the cylinder, perform the post-weld treatment, including non-destructive testing, post-weld heat treatment, and pressure resistance test to ensure the high quality of the kiln shell.