Industry Reports
Ball mill liner excessive wear reasons
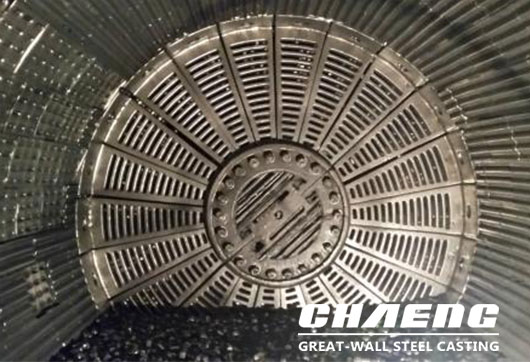
However, under the long-term operation of grinding media, the liner of the ball mill generally wears too fast. So what are the reasons that cause the ball mill liner to wear too fast?
1. Mutual wear between ball mill liner and steel balls
The ball mill liner and the steel ball are both vulnerable parts. During the grinding process, the ball mill steel balls and the material fall in a throwing motion in the cylinder. At this time, the ball mill liner and the steel balls, and the material will collide with each other. In continuous operation, the ball mill liner and steel balls will experience serious wear.
Coping method: Reasonable selection of ball mill liner and steel balls is one of the main ways to reduce the over-wear of the liner.
First, the relevant staff needs to understand the ratio of the ball mill liner to the steel balls and select the corresponding steel ball size and quantity according to the ratio.
Second, the ratio of materials and steel balls needs to be controlled.
Third, select the appropriate ball mill liner according to the mineral type, control the hardness of the ball mill liner and the steel ball, and make a reasonable match between the steel ball and the liner.
2. The material of the ball mill liner is unreasonable
The material of the ball mill liner and its heat treatment process are the keys to determining the mechanical properties of the liner. If the material of the liner is not selected properly, its fatigue strength and life will be greatly reduced. Not only can it not meet the requirements of the ball mill, but it may even undergo plastic deformation or cracking drum.
Coping method: Choose new wear-resistant liner materials. The commonly used ball mill liner materials include high manganese steel, high chromium steel, alloy steel, and wear-resistant rubber.
3. The heat treatment process of the ball mill liner is unreasonable
The unreasonable heat treatment of the ball mill liner will not only increase the wear of the liner but also affect the yield strength of the liner, causing the bolts of the ball mill to break under the action of large shearing force. In actual operations, the insufficient heat treatment of the liner of the ball mill, so the strengthening effect of the liner of the ball mill was not in place, the strength was low, and plastic deformation often occurred when hit by steel balls and materials. phenomenon.
Coping method: Pretreatment of the ball mill liner can effectively reduce the wear of the ball mill liner. The appropriate pretreatment process can be selected according to the material of the liner.
4. Abnormal operation of ball mill
When the ball mill is in an abnormal operating state, it will also bring adverse effects to the liner of the ball mill. When the ball mill is in normal operation, the steel balls are mixed with the materials. When the steel balls fall on the liner, they will form a barrier with the materials, play a buffering role, and gradually grind the materials. If the ball mill is operating under low load, the steel balls will directly impact the liner, causing serious wear and even breakage of the ball mill liner.
Coping method: Relevant staff should understand the operating status of the ball mill and control the operating status of the ball mill. When the ball mill is operating under a low load, the ore intake of the ball mill should be adjusted in time to ensure the grindability of the material.
In addition to the four reasons for wear described above, the design, manufacture, and installation of the liner of the ball mill are also some of the reasons that affect the excessive wear of the liner of the ball mill. In order to improve the efficiency of the use of the liner of the ball mill, it is necessary to analyze the reasons for the wear of the liner.