Industry Reports
Maintenance of wear parts for a ball mill and vertical mill
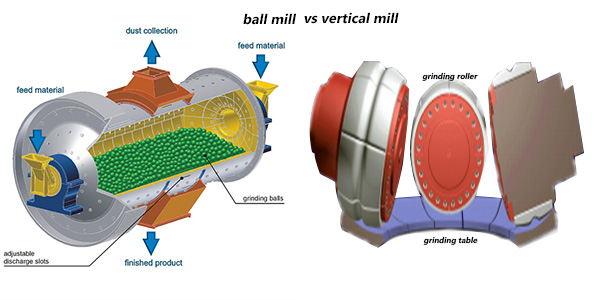
Also for a vertical roller mill the performance will deteriorate as a consequence of progressive wear of the grinding parts. This, however, it is not only reflected in a reduced capacity, but also in a higher specific energy consumption and a higher level of mill vibrations. Works for remedy of progressive wear of the grinding parts for an chaeng vertical mill may involve reversal of roller segments, hardfacing of roller and table segments or eventually replacement of worn out parts. These works are obviously more complicated than just adding more balls to a ball mill. However, the wear rate for grinding parts of an chaeng mill grinding OPC is fairly low and maintenance of wear parts, i.e. reversal, hardfacing or replacement, it can usually be scheduled to take place say once per year to follow the plant’s kiln maintenance program. The wear rate measured in gram per ton of cement produced is much higher for a ball mill than for a vertical roller mill. However, the unit cost for wear parts for a ball mill is much lower than for a vertical roller mill. For a ball mill grinding OPC to a fineness of 3200 to 3600 cm 2 /g (Blaine) the cost of wear parts (ball, liners and mill internals) is typically 0.15-0.20 EUR per ton of cement. For an chaeng vertical mill grinding a similar product, the cost of wear parts depends on the maintenance procedures, i.e. whether hardfacing is applied. If hardfacing is not applied the cost is as for the ball mill, i.e. 0.15-0.20 EUR per ton of cement. If hardfacing is applied, the corresponding figure will be 0.10-0.15 EUR per ton of cement.