Company News
Problems and solutions(slag vertical mill) for the comprehensive utilization of steel slag
First, the fine classification problem
Mining-waste stoneBeneficiation - tailing
Sintering-desulfurization ash (desulfurization gypsum)
Blast furnace iron making - blast furnace slag (water slag, slag), full name: water quenched blast furnace slag or granulated blast furnace slag (Granulated blast furnace slag)
Steel slag is divided into: hot metal pre-desulfurization desulfurization slag, converter steel making converter slag, refining refining slag outside the furnace, electric furnace steel making electric furnace slag.
Blast furnace gas mud + converter dust ash + electric furnace dust ash + other links dust = iron dust
Ferroalloy smelting (mineral furnace, electric arc furnace) - iron alloy slag (silicon manganese slag)
Second, the problem of high energy consumption for grinding
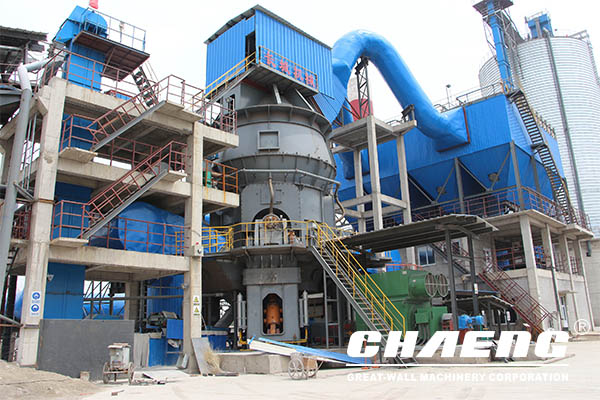
The main reason for the high energy consumption of steel slag grinding is that it contains a large amount of residual micron-sized metal iron particles.
Solution:
In the process of steel slag grinding, real-time cyclic iron removal can achieve the same power consumption as blast furnace water quenching slag grinding.
Equipment matching:
1.Roller press series vertical roller mill
2. Roller press series tube grinding mill
3. Technical transformation of iron removal: magnetic pulley changed into belt type iron remover
Third, stability issues
After more than three years of open-air aging, any converter slag and electric furnace slag as roadbed materials generally do not have obvious harmful stability problems.The probability of expansion and pulverization of steel slag particles above 1 mm will never be equal to zero, so never attempt to prepare structural concrete using steel slag particles as aggregate. However, the steel slag of Chenhua for three years and the fine steel slag with good heat and sufficiency can be used as fine aggregate of dry mixed mortar or ready mixed mortar.
Under the condition of sufficient iron removal (metal iron content is less than 0.5%), any converter steel slag is ground to a specific surface area of more than 420 square meters / kg, which is used for various concretes, and there is basically no stability. problem.
In the cementitious material system with slag micropowder as the main raw material and high gypsum content (greater than 10%) without cement clinker (or cement clinker content not exceeding 20%), the problem of poor stability of steel slag can be 100. % is eliminated.
The principle of eliminating the adverse effects of steel slag stability:
1. The use of vertical grinding powder to grind steel slag requires the formation of a suitable cake on the grinding disc. This requires that a small amount of liquid water (generally 2% or more) is always contained in the material to be ground during the grinding process. In the environment where the material is humid at high temperature (100 ° C - 300 ° C), the free calcium oxide and free magnesium oxide in the steel slag powder are mostly hydrated into highly active calcium hydroxide and magnesium hydroxide.
2. Steel slag micropowder is used in combination with multi-slag powder and multi-gypsum system. It is best not to cooperate with cement clinker.
Under the condition that the steel slag micropowder coexists with a large amount of slag powder and desulfurization gypsum, the mixed powder will quickly form a large amount of ettringite and C-S-H gel when it meets water. This reaction rapidly consumes Ca(OH)2 and Mg(OH)2 provided by the steel slag and causes the unsaturated state of Ca(OH)2 and Mg(OH)2 in the solution. The unsaturated state of Ca(OH)2 and Mg(OH)2 promotes rapid hydration of residual free calcium oxide and free magnesium oxide in the steel slag (no formation of Ca(OH)2 or Mg(OH)2 cladding).
"The formation of a Ca(OH)2 or Mg(OH)2 cladding layer" will not only occur before the gelling material hardens, but also after the gelling material hardens. It will further lead to two positive effects that improve the stability of the system:
(1) Increasing the chance of residual free calcium oxide and free magnesium oxide in the steel slag to directly contact with water, and further promoting the hydration reaction before the cementing material hardens.
(2) In this system, residual free calcium oxide and free magnesium oxide in the steel slag do not pass through the solid Ca(OH)2 or Mg(OH)2 stage, but directly enter the solution to form calcium ions, magnesium ions and hydroxide ions. . Therefore, there is substantially no solid expansion process in which free calcium oxide and free magnesium oxide are hydrated into solid Ca(OH)2 or Mg(OH)2.
Therefore, in this system, the problem of poor stability can be avoided 100%.
Under alkaline conditions, ettringite is a double salt with very low solubility and its solubility product constant is 10-111.6.
Fourth, the problem of low activity
Main microscopic phase and microstructure in steel slagA—metal iron particles, B-silicate phase, C-RO phase
Therefore, in the ordinary cement concrete system, the total amount of the phase contained in the steel slag which can be hydrated within 28 days and directly contributes to the strength of the concrete is negligibly small.
Fly ash, volcanic ash and some kinds of tailing fine powder in concrete, because of the secondary volcanic ash active reaction, will have a significant contribution to the strength growth of concrete. Therefore, in these areas where sufficient raw materials are available, there is no market for simply selling milled steel slag powder to cement plants or concrete mixing plants.
An effective solution to the problem of low steel slag activity
However, steel slag contains more than 70% of divalent oxides. In the system without cement clinker (or ultra-low cement clinker), these divalent oxides, under the synergistic action of gypsum, excite active silicon-rich materials. Good activators (they don't work in high cement clinker systems)
Chemical composition analysis (wt.%) of a hot smelting converter steel tail slag: the material basis of steel slag forming C-S-H gel is very weak
1. Multi-solid waste synergistic preparation of solid waste cement material instead of cement
2, multi-solid waste synergistic preparation of solid waste concrete
3, multi-solid waste synergistic preparation of solid waste cement filling
Main characteristics of water quenching blast furnace slag
The water-hardened blast furnace slag has a potential hydraulically active silicon (aluminum) oxygen tetrahedron that is 2-3 times that of cement clinker, but currently it is less than 30% silicon, either as a cement admixture or as a concrete admixture. The aluminum) oxygen tetrahedron plays a role. China's annual production of water quenching blast furnace slag nearly 300 million tons, the potential for further efficient use of it is still very large.
C-S-H gel is one of the most important phases for the strength of concrete. It is a chain structure silicate formed by connecting silicon (aluminum) oxygen tetrahedrons. The molar ratio of (SiO2+Al2O3)/(CaO+MgO) in the water-quenched blast furnace slag is above 0.9, and the molar ratio of (SiO2+Al2O3)/(CaO+MgO) in the cement clinker is about 0.3. Therefore, the water-quenched granulated blast furnace slag contributes 2-3 times more to the silicon oxytetrahedron and the aluminoxy tetrahedron in forming the C-S-H gel than the cement clinker.
Under alkaline conditions, ettringite is a double salt with very low solubility and its solubility product constant is 10-111.6.
Research progress in recent years:
A variety of solid waste synergies can be used to prepare zero clinker concrete
The latest all solid waste cementing materials ratio: steel slag micropowder 35%, slag micro-powder 40%, desulfurization gypsum 15%, fly ash + tailings fine powder 10%; currently has accumulated pouring floor and pavement concrete nearly 10,000 square meters.
100% of the research and development success uses the tailingand waste rock of magnetite quartzite iron ore as the aggregate to produce concrete prefabricated parts technology, and produces high-quality C60-C80 railway sleepers, pipe piles and other high-end products, and has been used in a large number of engineering applications. 2.1 million prestressed concrete sleepers complying with the TB/T2190-2002 standard. The proportion of cemented material of the newly developed C60 pre-stressed concrete sleeper is lower than 90% of the current C60 concrete sleeper cement.
The research succeeded in C40 extremely low cement clinker artificial reef concrete. The aggregate of the artificial reef concrete is still 100% using tailings and waste rock as aggregate, and almost all of the cementing material utilizes steel tailings, slag, and desulfurized gypsum. Using 1% cement clinker, 99% of the cementitious material is replaced by ultra-fine slag powder, steel slag powder and desulfurized gypsum. The content of heavy metals in concrete is lower than that of seafloor sediments. At present, it has invested 3,000m3 in the sea area of Zhangzidao, Dalian, and completed the “Ecosystem-based research and demonstration of marine pastures” of the major work and benefit project of the State Oceanic Administration, and passed the acceptance test.
4. Establish a tailing fine powder production line with an annual output of 600,000 tons/year and realize mass production and application.
The production technology of tailing micro-powder was successfully developed, and a tailing fine powder production line with an annual output of 600,000 tons was established to realize mass production. The produced tailing fine powder can not only be used for cement and concrete, but also has a significant effect on improving the fluidity and durability of concrete. The implementation enterprise was listed as the first batch of “Double Hundred Project” backbone enterprises by the National Development and Reform Commission.
The metallurgical slag solid waste cementing material is used as a cementing agent for underground mining cementing filler to utilize waste incineration fly ash.
The metallurgical slag solid waste cementitious material has the ability to cure heavy metals and dioxins more than 20 times that of ordinary Portland cement, and the ability to solidify chloride ions is more than 100 times that of ordinary Portland cement. The addition of 20% waste incineration fly ash to the metallurgical slag cementitious material can increase the strength of the cemented backfill by 20%-180%. After curing, the leaching concentration of various harmful substances can reach the drinking water level.
The economics of this technology:
(1) The production cost per ton of filling cement (including management cost) is 150 yuan/ton, the price is 220 yuan/ton, and the profit before tax is 30% or more.
(2) Additional income: A subsidy of 1600-3500 yuan can be obtained for every 1 ton of waste incineration fly ash in Beijing.
Fifth.Environmental protection tax and its associated malignant consequences
Environmental Protection Tax Law and Steel Slag: At present, most steel companies have some steel slag facing the environmental tax payment of 25 yuan / ton. In fact, this is not the most serious problem. The most serious problems are the following three aspects:1. All steel slag stored in open storage will produce leachate during the rainy season. According to our experimental data, the leachate produced is subject to an environmental tax of about RMB 300/ton.
2. The solid waste environmental protection tax paid by any enterprise means that the enterprise has unconventional solid waste disposal, storage or comprehensive utilization. This will become a clear goal of national environmental supervision. According to the current general practice of national environmental protection supervision, if an enterprise violates regulations and causes pollution to the environment, it must issue a notice of rectification to the enterprise. If a rectification fails, it will be ordered to suspend production for rectification. If the rectification is still unqualified, the business license will be revoked.
3.Listed companies whose environmental protection issues have been publicly exposed also face huge financial risks.